The mechanical properties of metals determine the range of usefulness
of the metal and establish the service that can be expected. Mechanical
properties are also used to help specify and identify metals. The most
common properties considered are strength, hardness, ductility, and impact
resistance.
Strength
The strength of a metal is its ability to withstand the action of external
forces without breaking. Tensile strength, also called ultimate strength,
is the maximum strength developed in a metal in a tension test. The
tension test is a method for determining the behavior of a metal under
an actual stretch loading. This test provides the elastic limit,
elongation, yield point, yield strength, tensile strength, and the
reduction in area. Tensile tests are normally taken at standardized
room temperatures but may also be made at elevated temperatures.
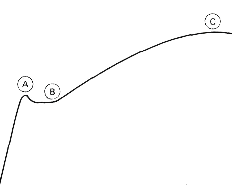
Many tensile testing machines are equipped to plot a curve which shows
the load or stress and the strain or movement that occurs during the test
operation. In the testing operation the load is increased gradually and
the specimen will stretch or elongate in proportion to the tensile load.
The specimen will elongate in direct proportion to the load during the
elastic portion of the curve to point A. At this point, the specimen
will continue to elongate but without an increase in the load. This is
known as the yield point of the steel and is the end of the elastic
portion. At any point up to point A if the load is eliminated, the
specimen will come back to its original dimension.
Yielding occurs from point A to point B and this is the area of
plastic deformation. If the load were eliminated at point B the
specimen would not go back to its original dimension but instead
take a permanent set. Beyond point B the load will have to be increased to
further stretch the specimen.
The load will increase to point C, which is the ultimate strength of the
material. At point C the specimen will break and the load is no longer
carried. The ultimate tensile strength of the material is obtained by
dividing the ultimate load by the cross-sectional area of the original
specimen. This provides the ultimate tensile strength in Newtons per
square millimeter (Mega Pascals, MPa) or pounds per square inch.
The yield stress or yield point is obtained by dividing the load at yield
or at point A by the original area. This provides a figure in pounds per
square inch or MPa. Extremely ductile metals do not have a yield point.
They stretch or yield at low loads. For these metals the yield point is
determined by the change in elongation. Two tenths of one percent
elongation is arbitrarily set as the yield point. The yield point
is the limit upon which designs are calculated.
Ductility
The ductility of a metal is the property that allows it to be stretched
or otherwise changed in shape without breaking and to retain the changed
shape after the load has been removed.
The ductility of a metal can be determined from the tensile test. This is
done by determining the percent of elongation. Gauge marks are made two
inches apart across the point where fracture will occur. The increase in
gauge length related to the original length times 100 is the percentage
of elongation. This is done by making center punch marks two inches apart
at the reduced section of the test coupon, testing the coupon, tightly
holding the two pieces together and re-measuring the distance between
the center punch marks. The original two inches is subtracted from the
measured length and the difference is divided by two and multiplied by
100 to obtain percentage of elongation.
Reduction of Area
Reduction of area is another measure of ductility and is obtained from
the tensile test by measuring the original cross-sectional area of the
specimen and relating it to the cross-sectional area after failure.
For a round specimen the diameter is measured and the cross-sectional
area is calculated. After the test bar is broken the diameter is measured
at the smallest point. The cross-sectional area is again calculated.
The difference in area is divided by the original area and multiplied
by 100 to give the percentage reduction of area. This figure is of
less importance than the elongation but is usually reported when the
mechanical properties of a metal are given.
The tensile test specimen also provides another property of metal
known as its modulus of elasticity, also called Young`s modulus. This
is the ratio of the stress to the elastic strain. It relates to the
slope of the curve to the yield point. The modulus of elasticity is
important to the designers and is incorporated in many design formulas.
Hardness
The hardness of a metal is defined as the resistance of a metal to
local penetration by harder substance. The hardness of metals is measured
by forcing a hardened steel ball or diamond into the surface of the
specimen, under a definite weight, in a hardness testing machine.
The Brinell is one of the more popular types of machines for measuring
hardness. It provides a Brinell hardness number (BHN), which is in
kilograms per square millimeter based on the load applied to the hardened
ball in kilograms and divided by the area of the impression left by the
ball in square millimeters.
There is several other hardness measuring systems. A popular machine is
the Rockwell hardness tester, which utilizes a diamond that is forced
into the surface of the specimen. Different loads are used to provide
different scaled. Smaller loads are used for softer materials. Another
method is by means of the Vickers hardness machine, which reads directly,
as a diamond is pressed into the surface of the metal. Another way is the
Shore scleroscope, which utilizes a small dropped weight which will bounce
from the surface of the metal providing a hardness measure.
Impact Resistance
Resistance of a metal to impacts is evaluated in terms of impact strength.
A metal may possess satisfactory ductility under static loads but may
fail under dynamic loads or impact.
Impact strength is most often determined by the Charpy test. It is sometimes
measured by the Izode test. Both types of tests use the same type of
pendulum-testing machine. The Charpy test specimen is a beam supported
at both ends and contains a notch in the center. The specimen is placed
on supports and struck with a pendulum on the side opposite the notch.
The accuracy and location of the notch is of extreme importance. There
are several types of Charpy specimens; the V-notch type is the most
popular.
The impact strength of a metal is determined by measuring the energy
absorbed in the fracture. This is equal to the weight of the pendulum
times the height at which the pendulum is released and the height to
which the pendulum swings after it has struck the specimen. In standard
metric practice, impact resistance is measured two ways. One, in Joules
based on energy absorbed and, two, in Joules per square centimeter of
the area of the fractured surface or the cross-sectional area under
the notch. In Anglo-Saxon terms the impact strength is the foot pounds
of energy absorbed.
List of Articles - Knowledge Base