The copper alloys may be endowed with a wide range of
properties by varying their composition and the mechanical
and heat treatment to which they are subjected. For this
reason they probably rank next to steel in importance to the
engineer.
The important alloys of copper and zinc from an industrial
point of view are the brasses comprised within certain limits
of zinc content. That portion of the constitutional diagram
which refers to these alloys is given in the Figure 1.
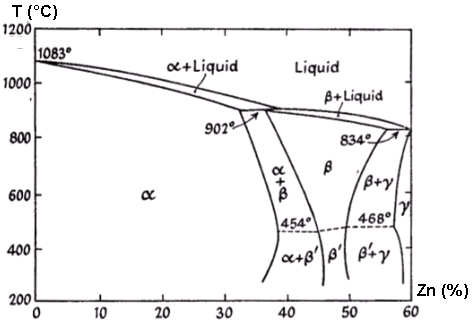
Figure 1. Constitutional Diagram of the Copper-Zinc Alloys
The addition of zinc to copper results in the formation of a
series of solid solutions which, in accordance with usual
practice, are referred to in order of diminishing copper
content as the a,
b, g,
etc., constituents. The diagram may be summarized as
follows:
Percentage composition
|
Constituent just below the freezing point
|
Constituent after slow cooling to 400°C
|
Copper
|
Zinc
|
100 to 67.5
|
0 to 32.5
|
a
|
a
|
67.5 to 63
|
32.5 to 37
|
a + b
|
a
|
63 to 61
|
37 to 39
|
b
|
a
|
61 to 55.5
|
39 to 45.5
|
b
|
a + b`
|
55.5 to 50
|
45.5 to 50
|
b
|
b`
|
50 to 43.5
|
50 to 56.5
|
b
|
b` + g
|
43.5 to 41
|
56.5 to 59
|
b + g
|
b` + g
|
Further changes in composition of the a
and b` phases below 400°C are
only observed after prolonged annealing.
There is a certain connection between the properties and
the microstructure which may be expressed in general
terms.
The tensile strength increases with increase in zinc
content, rises somewhat abruptly with the appearance of
b, and reaches a maximum at a
composition corresponding roughly to equal parts of
a and b.
It falls off rapidly at the appearance of the
g constituent.
Elongation rises to a maximum and begins to fall again
before the composition reaches the limit of the
a solution. It falls considerably
as the amount of b increases, and
is very small in the presence of g.
The a constituent shows the
greatest resistance to shock. This is diminished by the
presence of b, and the alloy
becomes extremely brittle when g
is present.
Hardness is greatly increased by the presence of
b and still further when
g appears.
Alloys containing a phase only
are specially suitable for cold working, and may be hot- or
cold rolled. Those containing a
and b will suffer very little
deformation without rupture in the cold rolling and may
only be hot rolled. The b
constituent may also be forged, rolled or hot extruded, but
alloys containing g should
invariably be avoided for any mechanical treatment.
Designation system of brasses
The brasses of industrial importance are often designated
by their copper and zinc content.
C 23000 - Red Brass (85 Cu, 15 Zn)
This alloy is used for ornaments and for cheap jewellery
which is to be gilded: it withstands cold-work, cupping, etc.
On account of the range of solidification, the cast material
has a dendritic structure.
If cooled very slowly or annealed, diffusion takes place,
yielding polyhedral grains of uniform composition. The
process of diffusion is assisted by mechanical deformation
of the grains by hot- or cold work followed by annealing.
The changes which occur in rolling and annealing are similar
to those described for 70:30 brass.
C 26000 - Cartridge Brass (70 Cu: 30 Zn)
This alloy, which is used widely for tubes, sheets and wires,
also shows a dendritic structure of the a
solid solution when chill fast. The b
constituent does not begin to appear in the cast structure
until the zinc exceeds 32% except in the presence of an
additional element like aluminum or tin.
After annealing, the alloy consists of homogeneous solid
solution, and it is specially suitable for cold-working. To
withstand this treatment, especially drawing, it is
necessary that the brass should be perfectly sound and free
from impurities.
Since high grade 70:30 brass is usually made from the purest
copper and zinc available without admixture of any but the
cleanest scrap, these impurities are chiefly inclusions of
dross (oxides or silicates) or charcoal. Such inclusions, if
present, frequently lead to failure of the material during
manufacture or in use. They become entrapped in the
solidifying metal, either by splashing or by rapid
solidification in moulds of small cross section.
It is a frequent procedure in casting brass to draw it into
rod to employ very long moulds of very small cross section,
in order to minimize subsequent mechanical treatment. Ingots
made in such moulds are most liable to contain inclusions
and to show piping to a great depth, resulting in central
unsoundness over a considerable length of the ingot. To
ensure soundness it is necessary to cast in a mould such that
the cross section is large enough to give relatively slow
cooling. The mould and stream of molten metal should be so
arranged as to avoid splashing; the dimensions of the mould
and speed of pouring should be such as to result in the ingot
solidifying from bottom upwards.
The effect of cold-work on the microstructure is to break
down the crystal grains by plastic deformation, and so crush
them into confused debris. Annealing after cold-work results
in recrystalization and subsequent crystal growth.
C 28000 - Muntz Metal (60 Cu: 40 Zn)
The molten metal begins to freeze at about 905°C, and
dendrites of the b solution are
formed. With sufficiently slow cooling through the range of
solidification the alloy consists of homogeneous
b constituent when just solid,
but, on cooling, this solution retains less copper and at
770°C the a constituent
separates from the homogeneous b
and increases in amount as the temperature falls. The
structure on reaching atmospheric temperature is therefore a
mixture of a and b,
the relative proportions of which may be controlled to some
extent by the rate of cooling.
For example, a thin section of 60:40 brass quenched from
800°C consists of homogeneous b.
With a larger section it is impossible to suppress completely
the separation of a, but a
specimen rapidly cooled from this temperature always contains
more b than a specimen more slowly
cooled. These microstructural characteristics are accompanied
by changes in mechanical properties which can be deduced from
the known hardness and brittleness of the b
constituent and the softness and ductility of the
a constituent.
Hot-rolled 60:40 brass, the rolling of which has been stopped
above 700°C, shows a uniform structure in longitudinal
and transverse directions. After the separation, the
a and b
constituents are each elongated in the direction of rolling,
giving the normal structure of rolled 60:40 brass. The lower
temperature of finishing, the smaller will be the grain
size. If, however, rolling is continued much below 600°C,
recrystalization does not keep pace with the deformation and
the metal is cold-worked.
Brazing solder (50 Cu: 50 Zn)
This alloy, if cooled sufficiently slowly through the range
of solidification, consists of homogeneous b
solution, which, however, may decompose on cooling if the
copper content is less than 50%. At atmospheric temperature
the b solution will retain a
maximum of just 50% of zinc if no impurities are present,
but any content of zinc over 50% causes the separation of
the g constituent, which increases
in amount as the temperature falls. Its presence renders the
alloy extremely hard and brittle.
List of Articles - Knowledge Base