Although pure iron is a weak material, steels cover a wide range of the strength
spectrum from low yield stress levels (around 200 MPa) to very high levels
(approaching 2000 MPa). These mechanical properties are usually achieved by the
combined use of several strengthening mechanisms, and in such circumstances it
is often difficult to quantify the different contributions to the strength.
These results should then be helpful in examining the behavior of more complex
steels.
Like other metals, iron can be strengthened by several basic mechanisms, the
most important of which are:
- Work hardening
- Solid solution strengthening by interstitial atoms
- Solid solution strengthening by substitutional atoms
- Refinement of grain size
- Dispersion strengthening, including lamellar and random dispersed structures.
The most distinctive aspect of strengthening of iron is the role of the interstitial
solutes carbon and nitrogen. These elements also play a vital part in interacting with
dislocations, and in combining preferentially with some of the metallic alloying
elements used in steels.
Work hardening
Work hardening is an important strengthening process in steel, particularly in
obtaining high strength levels in rod and wire, both in plain carbon and alloy steels.
For example, the tensile strength of a 0.05% C steel subjected to 95% reduction in
area by wire drawing, is raised by no less than 550 MPa while higher carbon steels
are strengthened by up to twice this amount. Indeed, without the addition of special
alloying elements, plain carbon steels can be raised to strength levels above 1500 MPa
simply by the phenomenon of work hardening.
Basic work on the deformation of iron has largely concentrated on the other end
of the strength spectrum, namely pure single crystals and polycrystals subjected
to small controlled deformations. The diversity of slip planes leads to rather
irregular wavy slip bands in deformed crystals, as the dislocations can readily
move from one type of plane to another by cross slip, provided they share a common
slip direction.
The yield stress of iron single crystals are very sensitive to both temperature
and strain rate and a similar dependence has been found for less pure polycrystalline
iron. Therefore, the temperature sensitivity cannot be attributed to interstitial
impurities. It is explained by the effect of temperature on the stress needed to
move free dislocations in the crystal, the Peierls-Nabarro stress.
Solid solution strengthening by interstitials
The formation of interstitial atmospheres at dislocations requires diffusion of the
solute. As both carbon and nitrogen diffuse much more rapidly in iron than
substitutional solutes, it is not surprising that strain ageing can take place
readily in the range from 20°C to 150°C. Consequently the atmosphere condenses
to form rows of interstitial atoms along the cores of the dislocations. These arise
because the temperature is high enough to allow interstitial atoms to diffuse during
deformation, and to form atmospheres around dislocations generated throughout the
stress-strain curve. Steels tested under these conditions also show low ductility`s,
due partly to the high dislocation density and partly to the nucleation of carbide
particles on the dislocations where the carbon concentration is high. The phenomenon
is often referred to as blue brittleness, blue being the interference color of the
steel surface when oxidized in this temperature range.
The break away of dislocations from their carbon atmospheres as a cause of the sharp
yield point became a controversial aspect of the theory because it was found that
the provision of free dislocations, for example, by scratching the surface of a
specimen, did not eliminate the sharp yield point. An alternative theory was developed
which assumed that, once condensed carbon atmospheres are formed in iron, the
dislocations remain locked, and the yield phenomena arise from the generation and
movement of newly formed dislocations.
To summarize, the occurrence of a sharp yield point depends on the occurrence of a
sudden increase in the number of mobile dislocations. However, the precise mechanism
by which this takes place will depend on the effectiveness of the locking of the
pre-existing dislocations. If the pinning is weak, then the yield point can arise
as a result of unpinning. However, if the dislocations are strongly locked, either
by interstitial atmospheres or precipitates, the yield point will result from the
rapid generation of new dislocations.
Under conditions of dynamic strain ageing, where atmospheres of carbon atoms form
continuously on newly-generated dislocations, it would be expected that a higher
density of dislocations would be needed to complete the deformation, if it is assumed
that most dislocations which attract carbon atmospheres are permanently locked in
position.
Strengthening at high interstitial concentrations
Austenite can take into solid solution up to 10% carbon, which can be retained in
solid solution by rapid quenching. However, in these circumstances the phase
transformation takes place, not to ferrite but to a tetragonal structure referred
to as martensite. This phase forms as a result of diffusion less shear transformation
leading to characteristic laths or plates.
If the quench is sufficiently rapid, the martensite is essentially a supersaturated
solid solution of carbon in a tetragonal iron matrix, and as the carbon concentration
can be greatly in excess of the equilibrium concentration in ferrite, the strength is
raised very substantially. High carbon martensites are normally very hard but brittle,
the yield strength reaching as much as 1500 MPa; much of this increase can be directly
attributed to increased interstitial solid solution hardening, but there is also a
contribution from the high dislocation density, which is characteristic of martensitic
transformations in iron-carbon alloys.
Substitutional solid solution strengthening of iron
Many metallic elements form solid solutions in γ- and α-iron. These are
invariably substitutional solid solutions, but for a constant atomic concentration
of alloying elements there are large variations in strength. Using single crystal
data for several metals, Fig. 1 shows that an element such as vanadium has a weak
strengthening effect on α-iron at low concentrations (< 2%), while silicon
and molybdenum are much more effective strengthened. Other data indicates that
phosphorus; manganese, nickel and copper are also effective strengtheners. However,
it should be noted that the relative strengthening might alter with the temperature
of testing, and with the concentrations of interstitial solutes present in the
steels.
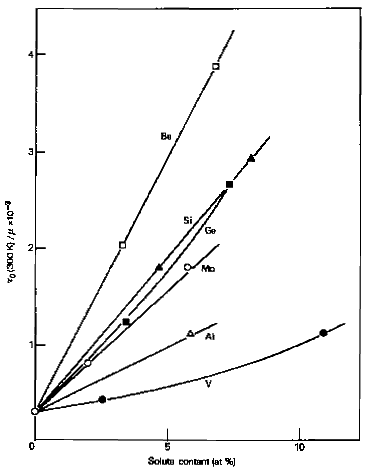
Figure 1. Solid solution strengthening of iron crystals by substitutional
solutes. Ratio of the critical resolved shear stress τ0 to shear
modulus μ as a function of atomic concentration.
The strengthening achieved by substitutional solute atoms is, in general, greater
the larger the difference in atomic size of the solute from that of iron, applying
the Hume-Rothery size effect. However, from the work of Fleischer and Takeuchi it
is apparent that differences in the elastic behavior of solute and solvent atoms
are also important in determining the overall strengthening achieved.
In practical terms, the contribution to strength from solid solution effects is
superimposed on hardening from other sources, e.g. grain size and dispersions. Also
it is a strengthening increment, like that due to grain size, which need not adversely
affect ductility. In industrial steels, solid solution strengthening is a far from
negligible factor in the overall strength, where it is achieved by a number of
familiar alloying elements, e.g. manganese, silicon, nickel, molybdenum, several of
which are frequently present in a particular steel and are additive in their effect.
These alloying elements arc usually added for other reasons, e.g. Si to achieve
deoxidation, Mn to combine with sulphur or Mo to promote hardenability. Therefore,
the solid solution hardening contribution can be viewed as a useful bonus.
Grain size
The refinement of the grain size of ferrite provides one of the most important
strengthening routes in the heal treatment of steels. The grain size effect on
the yield stress can therefore be explained by assuming that a dislocation source
operates within a crystal causing dislocations to move and eventually to pile up at
the grain boundary. The pile-up causes a stress to be generated in the adjacent grain,
which, when it reaches a critical value, operates a new source in that grain.
In this way, the yielding process is propagated from grain to grain. The grain size
determines the distance dislocations have to move to form grain boundary pile-ups,
and thus the number of dislocations involved. With large grain sizes, the pile-ups
will contain larger numbers of dislocations, which will in turn cause higher stress
concentrations in neighboring grains.
In practical terms, the finer the grain size, the higher the resulting yield
stress and, as a result, in modern steel working much attention is paid to the final
ferrite grain size. While a coarse grain size of d-1/2 = 2, i.e. d = 0.25 mm,
gives a yield stress in mild steels of around 100 MPa, grain refinement to
d-1/2 = 20, i.e. d = 0.0025 mm, raises the yield stress to over 500 MPa,
so that achieving grain sizes in the range 2-10 μm is extremely worthwhile.
Dispersion strengthening
In all steels there is normally more than one phase present, and indeed it is
often the case that several phases can be recognized in the microstructure. The matrix,
which is usually ferrite (bcc structure) or austenite (fcc structure) strengthened
by grain size refinement and by solid solution additions, is further strengthened,
often to a considerable degree, by controlling the dispersions of the other phases
in the microstructure. The commonest other phases are carbides formed as a result
of the low solubility of carbon in α-iron. In plain carbon steels this carbide
is normally Fe3C (cementite), which can occur, in a wide range of structures
from coarse lamellar form (pearlite), to fine rod or spheroidal precipitates
(tempered steels). In alloy steels, the same range of structures is encountered,
except that in many cases iron carbide is replaced by other carbides, which are
thermodynamically more stable. Other dispersed phases which are encountered include
nitrides, intermetallic compounds, and, in cast irons, graphite.
Most dispersions lead to strengthening, but often they can have adverse effects on
ductility and toughness. In fine dispersions (where ideally small spheres are randomly
dispersed in a matrix) are well-defined relationships between the yield stress, or
initial flow stress, and the parameters of the dispersion.
These relationships can be applied to simple dispersions sometimes found in steels,
particularly after tempering, when, in plain carbon steels, the structure consists
of spheroidal cementite particles in a ferritic matrix. However, they can provide
approximations in less ideal cases, which are the rule in steels, where the
dispersions vary over the range from fine rods and plates to irregular polyhedral.
Perhaps the most familiar structure in steels is that of the eutectoid pearlite,
usually a lamellar mixture of ferrite and cementite. This can be considered as an
extreme form of dispersion of one phase in another, and undoubtedly provides a
useful contribution to strengthening.
An overall view
Strength in steels arises from several phenomena, which usually contribute
collectively to the observed mechanical properties. The heat treatment of steels
is aimed at adjusting these contributions so that the required balance of mechanical
properties is achieved. Fortunately the γ/α phase change allows great
variations in microstructure to be produced, so that a wide range of mechanical
properties can be obtained even in plain carbon steels. The additional use of
metallic alloying elements, primarily as a result of their influence on the
transformation, provides an even greater control over microstructure, with
consequent benefits in the mechanical properties.
List of Articles - Knowledge Base